Nos últimos anos, graças ao rápido desenvolvimento da nova indústria energética, a soldagem a laser penetrou rapidamente em toda a nova indústria energética devido às suas vantagens rápidas e estáveis. Entre eles, os equipamentos de soldagem a laser são responsáveis pela maior proporção de aplicações em toda a nova indústria de energia.
Soldagem a laserrapidamente se tornou a primeira escolha em todas as esferas da vida devido à sua velocidade rápida, grande profundidade e pequena deformação. De soldas por pontos a soldas de topo, soldas de acúmulo e vedação,soldagem a laserfornece precisão e controle incomparáveis. Desempenha um papel importante na produção e fabricação industrial, incluindo indústria militar, assistência médica, aeroespacial, peças automotivas 3C, chapas metálicas mecânicas, novas energias e outras indústrias.
Comparada com outras tecnologias de soldagem, a soldagem a laser tem vantagens e desvantagens exclusivas.
Vantagem:
1. Velocidade rápida, grande profundidade e pequena deformação.
2. A soldagem pode ser realizada em temperatura normal ou sob condições especiais, e o equipamento de soldagem é simples. Por exemplo, um feixe de laser não flutua num campo eletromagnético. Os lasers podem soldar em ambientes de vácuo, ar ou certos gases, e podem soldar materiais que são através de vidro ou transparentes ao feixe de laser.
3. Pode soldar materiais refratários, como titânio e quartzo, e também pode soldar materiais diferentes com bons resultados.
4. Depois que o laser é focado, a densidade de potência é alta. A proporção de aspecto pode chegar a 5:1 e até 10:1 ao soldar dispositivos de alta potência.
5. Micro soldagem pode ser realizada. Depois que o feixe de laser é focado, um pequeno ponto pode ser obtido e posicionado com precisão. Pode ser aplicado à montagem e soldagem de peças micro e pequenas para obter produção em massa automatizada.
6. Pode soldar áreas de difícil acesso e realizar soldagem de longa distância sem contato, com grande flexibilidade. Especialmente nos últimos anos, a tecnologia de processamento a laser YAG adotou a tecnologia de transmissão de fibra óptica, o que permitiu que a tecnologia de soldagem a laser fosse promovida e aplicada de forma mais ampla.
7. O feixe de laser é fácil de dividir no tempo e no espaço, e vários feixes podem ser processados em vários locais simultaneamente, proporcionando condições para uma soldagem mais precisa.
Defeito:
1. A precisão de montagem da peça de trabalho deve ser alta e a posição da viga na peça de trabalho não pode ser desviada significativamente. Isso ocorre porque o tamanho do ponto do laser após o foco é pequeno e a costura de solda é estreita, dificultando a adição de materiais de metal de adição. Se a precisão de montagem da peça de trabalho ou a precisão de posicionamento da viga não atender aos requisitos, é provável que ocorram defeitos de soldagem.
2. O custo dos lasers e sistemas relacionados é alto e o investimento único é grande.
Defeitos comuns de soldagem a laserna fabricação de baterias de lítio
1. Porosidade de soldagem
Defeitos comuns emsoldagem a lasersão poros. A poça de fusão da soldagem é profunda e estreita. Durante o processo de soldagem a laser, o nitrogênio invade a poça de fusão vinda de fora. Durante o processo de resfriamento e solidificação do metal, a solubilidade do nitrogênio diminui com a diminuição da temperatura. Quando o metal fundido da poça esfria para começar a cristalizar, a solubilidade cairá acentuada e repentinamente. Neste momento, uma grande quantidade de gás precipitará para formar bolhas. Se a velocidade de flutuação das bolhas for menor que a velocidade de cristalização do metal, serão gerados poros.
Em aplicações na indústria de baterias de lítio, frequentemente descobrimos que os poros são particularmente prováveis de ocorrer durante a soldagem do eletrodo positivo, mas raramente ocorrem durante a soldagem do eletrodo negativo. Isso ocorre porque o eletrodo positivo é feito de alumínio e o eletrodo negativo é feito de cobre. Durante a soldagem, o alumínio líquido na superfície condensou-se antes que o gás interno transbordasse completamente, evitando que o gás transbordasse e formasse furos grandes e pequenos. Estômatos pequenos.
Além das causas dos poros mencionadas acima, os poros também incluem ar externo, umidade, óleo superficial, etc. Além disso, a direção e o ângulo do sopro de nitrogênio também afetarão a formação de poros.
E como reduzir a ocorrência de poros de soldagem?
Primeiro, antessoldagem, as manchas de óleo e impurezas na superfície dos materiais recebidos precisam ser limpas a tempo; na produção de baterias de lítio, a inspeção do material recebido é um processo essencial.
Em segundo lugar, o fluxo do gás de proteção deve ser ajustado de acordo com fatores como velocidade de soldagem, potência, posição, etc., e não deve ser nem muito grande nem muito pequeno. A pressão da capa protetora deve ser ajustada de acordo com fatores como a potência do laser e a posição do foco, e não deve ser nem muito alta nem muito baixa. O formato do bico da capa protetora deve ser ajustado de acordo com o formato, direção e outros fatores da solda, para que a capa protetora possa cobrir uniformemente a área de soldagem.
Terceiro, controle a temperatura, a umidade e a poeira do ar na oficina. A temperatura ambiente e a umidade afetarão o teor de umidade na superfície do substrato e do gás protetor, o que por sua vez afetará a geração e o escape de vapor d'água na poça de fusão. Se a temperatura ambiente e a umidade forem muito altas, haverá muita umidade na superfície do substrato e no gás protetor, gerando grande quantidade de vapor d'água, resultando em poros. Se a temperatura e a umidade ambiente forem muito baixas, haverá pouca umidade na superfície do substrato e no gás de proteção, reduzindo a geração de vapor d'água, reduzindo assim os poros; deixe o pessoal de qualidade detectar o valor alvo de temperatura, umidade e poeira na estação de soldagem.
Quarto, o método de oscilação do feixe é usado para reduzir ou eliminar poros na soldagem de penetração profunda a laser. Devido à adição de oscilação durante a soldagem, a oscilação alternativa da viga para a costura de solda causa a refusão repetida de parte da costura de solda, o que prolonga o tempo de residência do metal líquido na poça de soldagem. Ao mesmo tempo, a deflexão do feixe também aumenta a entrada de calor por unidade de área. A relação profundidade-largura da solda é reduzida, o que favorece o surgimento de bolhas, eliminando assim os poros. Por outro lado, o balanço da viga faz com que o pequeno orifício balance de acordo, o que também pode fornecer uma força de agitação para a poça de soldagem, aumentar a convecção e a agitação da poça de soldagem e ter um efeito benéfico na eliminação dos poros.
Quinto, a frequência de pulso, a frequência de pulso refere-se ao número de pulsos emitidos pelo feixe de laser por unidade de tempo, o que afetará a entrada de calor e o acúmulo de calor na poça fundida e, em seguida, afetará o campo de temperatura e o campo de fluxo no fundido piscina. Se a frequência de pulso for muito alta, isso levará a uma entrada excessiva de calor na poça fundida, fazendo com que a temperatura da poça fundida seja muito alta, produzindo vapor metálico ou outros elementos que são voláteis em altas temperaturas, resultando em poros. Se a frequência de pulso for muito baixa, isso levará ao acúmulo insuficiente de calor na poça fundida, fazendo com que a temperatura da poça fundida seja muito baixa, reduzindo a dissolução e o escape de gás, resultando em poros. De modo geral, a frequência de pulso deve ser escolhida dentro de uma faixa razoável com base na espessura do substrato e na potência do laser, e evitar ser muito alta ou muito baixa.
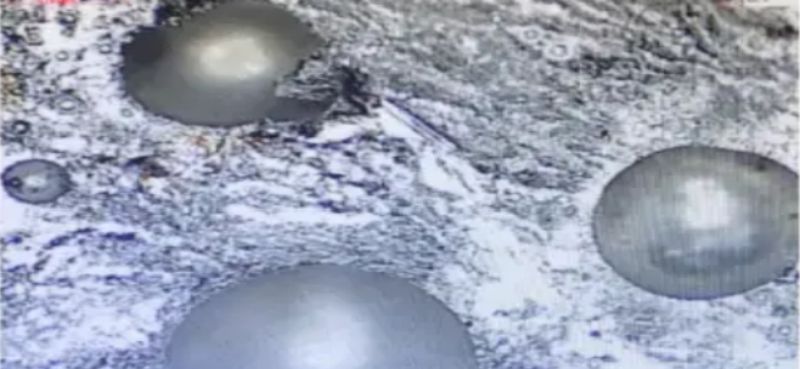
Furos de soldagem (soldagem a laser)
2. Respingos de solda
Os respingos gerados durante o processo de soldagem, a soldagem a laser afetarão seriamente a qualidade da superfície da solda e poluirão e danificarão a lente. O desempenho geral é o seguinte: após a conclusão da soldagem a laser, muitas partículas metálicas aparecem na superfície do material ou peça de trabalho e aderem à superfície do material ou peça de trabalho. O desempenho mais intuitivo é que ao soldar no modo galvanômetro, após um período de uso da lente protetora do galvanômetro, haverá poços densos na superfície, e esses poços são causados por respingos de soldagem. Depois de muito tempo, é fácil bloquear a luz e haverá problemas com a soldagem da luz, resultando em uma série de problemas como soldagem quebrada e soldagem virtual.
Quais são as causas dos respingos?
Primeiro, a densidade de potência, quanto maior a densidade de potência, mais fácil é gerar respingos, e os respingos estão diretamente relacionados à densidade de potência. Este é um problema centenário. Pelo menos até agora, a indústria não conseguiu resolver o problema dos salpicos, podendo apenas dizer que foi ligeiramente reduzido. Na indústria de baterias de lítio, os respingos são os maiores culpados do curto-circuito da bateria, mas não foram capazes de resolver a causa raiz. O impacto dos respingos na bateria só pode ser reduzido do ponto de vista da proteção. Por exemplo, um círculo de portas de remoção de poeira e tampas protetoras são adicionados ao redor da peça de soldagem, e fileiras de facas de ar são adicionadas em círculos para evitar o impacto de respingos ou até mesmo danos à bateria. Pode-se dizer que a destruição do meio ambiente, dos produtos e dos componentes ao redor da estação de soldagem esgotou os meios.
Quanto à resolução do problema dos respingos, só se pode dizer que a redução da energia de soldagem ajuda a reduzir os respingos. A redução da velocidade de soldagem também pode ajudar se a penetração for insuficiente. Mas em alguns requisitos especiais de processo, tem pouco efeito. É o mesmo processo, diferentes máquinas e diferentes lotes de materiais têm efeitos de soldagem completamente diferentes. Portanto, existe uma regra não escrita na nova indústria energética, um conjunto de parâmetros de soldagem para uma peça de equipamento.
Em segundo lugar, se a superfície do material processado ou da peça de trabalho não for limpa, manchas de óleo ou poluentes também causarão respingos graves. Neste momento, o mais fácil é limpar a superfície do material processado.
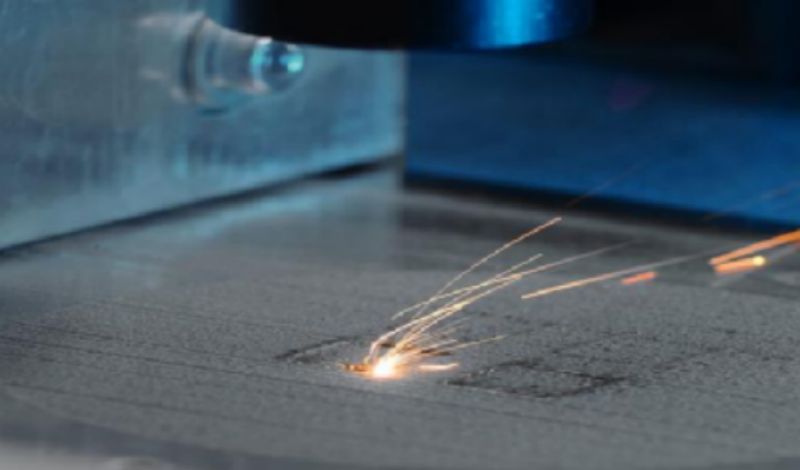
3. Alta refletividade da soldagem a laser
De modo geral, alta reflexão refere-se ao fato de que o material de processamento tem uma pequena resistividade, uma superfície relativamente lisa e uma baixa taxa de absorção para lasers infravermelhos próximos, o que leva a uma grande quantidade de emissão de laser, e porque a maioria dos lasers são usados na vertical Devido ao material ou a uma pequena inclinação, a luz laser de retorno entra novamente na cabeça de saída e até mesmo parte da luz de retorno é acoplada à fibra transmissora de energia e é transmitida de volta ao longo da fibra para o interior do laser, fazendo com que os componentes principais dentro do laser continuem em alta temperatura.
Quando a refletividade é muito alta durante a soldagem a laser, as seguintes soluções podem ser tomadas:
3.1 Use revestimento anti-reflexo ou trate a superfície do material: revestir a superfície do material de soldagem com um revestimento anti-reflexo pode efetivamente reduzir a refletividade do laser. Este revestimento é geralmente um material óptico especial com baixa refletividade que absorve a energia do laser em vez de refleti-la de volta. Em alguns processos, como soldagem de coletor de corrente, conexão suave, etc., a superfície também pode ser gofrada.
3.2 Ajuste o ângulo de soldagem: Ao ajustar o ângulo de soldagem, o feixe de laser pode incidir no material de soldagem em um ângulo mais apropriado e reduzir a ocorrência de reflexão. Normalmente, fazer com que o feixe de laser incida perpendicularmente à superfície do material a ser soldado é uma boa forma de reduzir os reflexos.
3.3 Adicionando absorvente auxiliar: Durante o processo de soldagem, uma certa quantidade de absorvente auxiliar, como pó ou líquido, é adicionada à solda. Esses absorvedores absorvem a energia do laser e reduzem a refletividade. O absorvente apropriado precisa ser selecionado com base nos materiais de soldagem específicos e nos cenários de aplicação. Na indústria de baterias de lítio, isso é improvável.
3.4 Use fibra óptica para transmitir o laser: Se possível, a fibra óptica pode ser usada para transmitir o laser para a posição de soldagem para reduzir a refletividade. As fibras ópticas podem guiar o feixe de laser até a área de soldagem para evitar a exposição direta à superfície do material de soldagem e reduzir a ocorrência de reflexos.
3.5 Ajustando os parâmetros do laser: Ao ajustar parâmetros como potência do laser, distância focal e diâmetro focal, a distribuição da energia do laser pode ser controlada e os reflexos podem ser reduzidos. Para alguns materiais reflexivos, reduzir a potência do laser pode ser uma forma eficaz de reduzir os reflexos.
3.6 Use um divisor de feixe: Um divisor de feixe pode guiar parte da energia do laser para o dispositivo de absorção, reduzindo assim a ocorrência de reflexos. Os dispositivos de divisão de feixe geralmente consistem em componentes ópticos e absorvedores e, selecionando componentes apropriados e ajustando o layout do dispositivo, pode-se obter menor refletividade.
4. Corte inferior de soldagem
No processo de fabricação de baterias de lítio, quais processos têm maior probabilidade de causar subcotação? Por que ocorre a subcotação? Vamos analisar isso.
Corte inferior, geralmente as matérias-primas de soldagem não estão bem combinadas entre si, a folga é muito grande ou a ranhura aparece, a profundidade e a largura são basicamente maiores que 0,5 mm, o comprimento total é maior que 10% do comprimento da solda, ou maior que o padrão de processo do produto, o comprimento solicitado.
Em todo o processo de fabricação da bateria de lítio, é mais provável que ocorra subcotação e geralmente é distribuído na pré-soldagem e soldagem de vedação da placa de cobertura cilíndrica e na pré-soldagem e soldagem de vedação da placa de cobertura quadrada de alumínio. A principal razão é que a placa de cobertura de vedação precisa cooperar com o invólucro para soldagem, o processo de correspondência entre a placa de cobertura de vedação e o invólucro é propenso a lacunas excessivas de solda, ranhuras, colapso, etc., por isso é particularmente propenso a cortes inferiores .
Então, o que causa a subcotação?
Se a velocidade de soldagem for muito rápida, o metal líquido atrás do pequeno furo apontando para o centro da solda não terá tempo de se redistribuir, resultando em solidificação e corte inferior em ambos os lados da solda. Diante da situação acima, precisamos otimizar os parâmetros de soldagem. Simplificando, são repetidos experimentos para verificar vários parâmetros e continuar fazendo DOE até que os parâmetros apropriados sejam encontrados.
2. Lacunas de solda excessivas, ranhuras, colapsos, etc. de materiais de soldagem reduzirão a quantidade de metal fundido preenchendo as lacunas, tornando mais provável a ocorrência de cortes inferiores. É uma questão de equipamentos e matérias-primas. Se as matérias-primas de soldagem atendem aos requisitos de material de entrada de nosso processo, se a precisão do equipamento atende aos requisitos, etc. A prática normal é torturar e espancar constantemente os fornecedores e os responsáveis pelo equipamento.
3. Se a energia cair muito rapidamente no final da soldagem a laser, o pequeno orifício pode entrar em colapso, resultando em corte local. A combinação correta de potência e velocidade pode prevenir eficazmente a formação de rebaixos. Como diz o velho ditado, repita os experimentos, verifique vários parâmetros e continue o DOE até encontrar os parâmetros corretos.
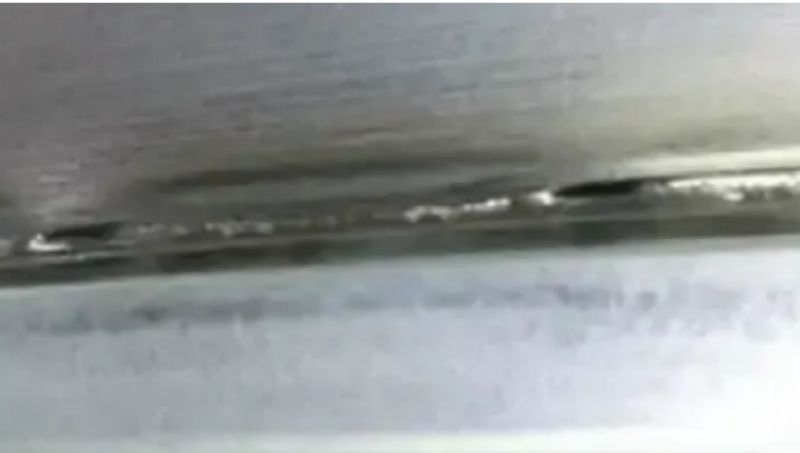
5. Colapso do centro de solda
Se a velocidade de soldagem for lenta, a poça fundida será maior e mais larga, aumentando a quantidade de metal fundido. Isso pode dificultar a manutenção da tensão superficial. Quando o metal fundido fica muito pesado, o centro da solda pode afundar e formar depressões e buracos. Neste caso, a densidade de energia precisa ser reduzida adequadamente para evitar o colapso da poça de fusão.
Noutra situação, a folga de soldadura apenas forma um colapso sem causar perfuração. Este é sem dúvida um problema de ajuste à pressão do equipamento.
Uma compreensão adequada dos defeitos que podem ocorrer durante a soldagem a laser e das causas dos diferentes defeitos permite uma abordagem mais direcionada para resolver quaisquer problemas anormais de soldagem.
6. Rachaduras de solda
As trincas que aparecem durante a soldagem a laser contínua são principalmente trincas térmicas, como trincas de cristal e trincas de liquefação. A principal causa destas fissuras são as grandes forças de retração geradas pela solda antes que ela se solidifique completamente.
Existem também as seguintes razões para rachaduras na soldagem a laser:
1. Projeto de solda irracional: O projeto inadequado da geometria e do tamanho da solda pode causar concentração de tensão de soldagem, causando rachaduras. A solução é otimizar o projeto da solda para evitar a concentração de tensões de soldagem. Você pode usar soldas deslocadas apropriadas, alterar o formato da solda, etc.
2. Incompatibilidade dos parâmetros de soldagem: A seleção inadequada dos parâmetros de soldagem, como velocidade de soldagem muito rápida, potência muito alta, etc., pode levar a mudanças desiguais de temperatura na área de soldagem, resultando em grandes tensões de soldagem e rachaduras. A solução é ajustar os parâmetros de soldagem para corresponder ao material específico e às condições de soldagem.
3. Má preparação da superfície de soldagem: A falha na limpeza e pré-tratamento adequado da superfície de soldagem antes da soldagem, como remoção de óxidos, graxa, etc., afetará a qualidade e a resistência da solda e facilmente causará rachaduras. A solução é limpar e pré-tratar adequadamente a superfície de soldagem para garantir que impurezas e contaminantes na área de soldagem sejam tratados de forma eficaz.
4. Controle inadequado da entrada de calor de soldagem: O mau controle da entrada de calor durante a soldagem, como temperatura excessiva durante a soldagem, taxa de resfriamento inadequada da camada de soldagem, etc., levará a mudanças na estrutura da área de soldagem, resultando em rachaduras . A solução é controlar a temperatura e a taxa de resfriamento durante a soldagem para evitar superaquecimento e resfriamento rápido.
5. Alívio de tensão insuficiente: O tratamento de alívio de tensão insuficiente após a soldagem resultará em alívio de tensão insuficiente na área soldada, o que facilmente levará a rachaduras. A solução é realizar um tratamento adequado de alívio de tensões após a soldagem, como tratamento térmico ou tratamento vibratório (motivo principal).
Quanto ao processo de fabricação das baterias de lítio, quais processos têm maior probabilidade de causar rachaduras?
Geralmente, rachaduras são propensas a ocorrer durante a soldagem de vedação, como soldagem de vedação de invólucros de aço cilíndrico ou de alumínio, soldagem de vedação de invólucros quadrados de alumínio, etc. Além disso, durante o processo de embalagem do módulo, a soldagem do coletor de corrente também é propensa para rachaduras.
Claro, também podemos usar fio de enchimento, pré-aquecimento ou outros métodos para reduzir ou eliminar essas fissuras.
Horário da postagem: 01/09/2023